System Summaries
Whole System Summary, BEFORE Upgrade Project
- Two interconnected Sides of the vacuum distribution system.
- Five (5) ROGERS VACUUM SYSTEMS online and running at 100%.
- Model Number: RVS.LR.2K5
- Each vacuum pump motor is 150 Horsepower.
- Unable to meet Target SET-POINT of 23.5 “HgV in many barometric conditions.
- All units online and running means Zero Redundancy installed in place.
- System Capacity at typical Operating Point … ~8500 ACFM
- (Theoretical) System Capacity at Set-Point … ~4000 ACFM
- Approximate Power Consumption … 4,900,000 kWHrs/year
- Nominal Chilled Water Consumption … 155 Million gallons/year
System Summary, AFTER Project
- Four (4) ROGERS VACUUM SYSTEMS online and running, now EACH at 50%.
- Able to meet (AND EXCEED) Target SET-POINT of 23.5 “HgV
- …in ALL barometric conditions.
- Average of N+2 Redundancy installed in place.
- …often N+3 in periods of barometric high pressure.
- Current Capacity Operating at Set-Point … ~9300 ACFM
- Maximum Design System Capacity AT Set-Point … ~17,500 ACFM
- Approximate Current Power Consumption … 2,800,000 kWHrs/year
- Approximate Chilled Water Consumption … 68 Million gallons/year
Summary of NET GAINS
- On average, (2 ½) 150 HP ROGERS VACUUM SYSTEMS have been “given back” to Sam’s Facility for future use and immediate installed redundancy.
- Able to meet (AND EXCEED) Target Set-Point of 23.5 “HgV
- …in ALL barometric conditions.
- Average of N+2 Redundancy installed in place.
- …often N+3 in periods of barometric high pressure.
- Currently operating at approximately 53% of total new system capacity
- Approximate Annual Power Savings … 2,100,000 kWHrs/year
- Approximate Annual Chilled Water Savings … 87,000,000 gallons/year
Customer Backstory
Awhile back a loyal client, we’ll call him Sam, at an electronics manufacturer in New Mexico called in with a problem. Sam had recently noticed that their fifth of five 150 Horsepower Process Vacuum (PVAC) pumps had been starting to turn on and run more frequently. They’d been recently adding some Process Vacuum demands onto their centralized system here and there and had plans for even more in the near future.
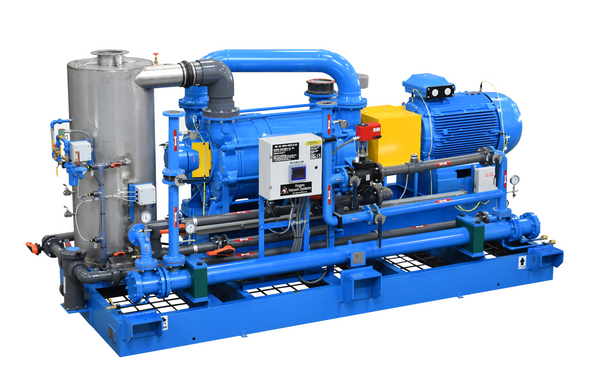
Our Engineered System Solutions Are Built To Your Specifications
After pulling some historical trends, Sam discovered that the fifth PVAC pump appeared to have been running with some regularity already. As he dug into the data, things just got worse. Often times, whether four or five pumps were running, they were also not able to meet their system setpoint.
Electronics applications typically run their tooling requiring Process Vacuum based on differential pressure from barometric; that is, they control their PVAC pumps to “Inches of Mercury Vacuum”. This is because the parts and pieces being manipulated by vacuum are of certain sizes, shapes, and weights. If the differential pressure across the part is not great enough, then the tooling will fail and results in a loss of product, adverse impact to quality, and production downtime. This amounts to millions of dollars in unrecoverable expense.
With their PVAC system no longer fully redundant and intermittently unable to provide production with its requirements, something had to be done. When Sam called, his request of us to solve his dilemma was the solution that most in his shoes would choose, “We’re out of vacuum! We need another vacuum pump. Can I get price and availability for an identical RVS.LR system?”
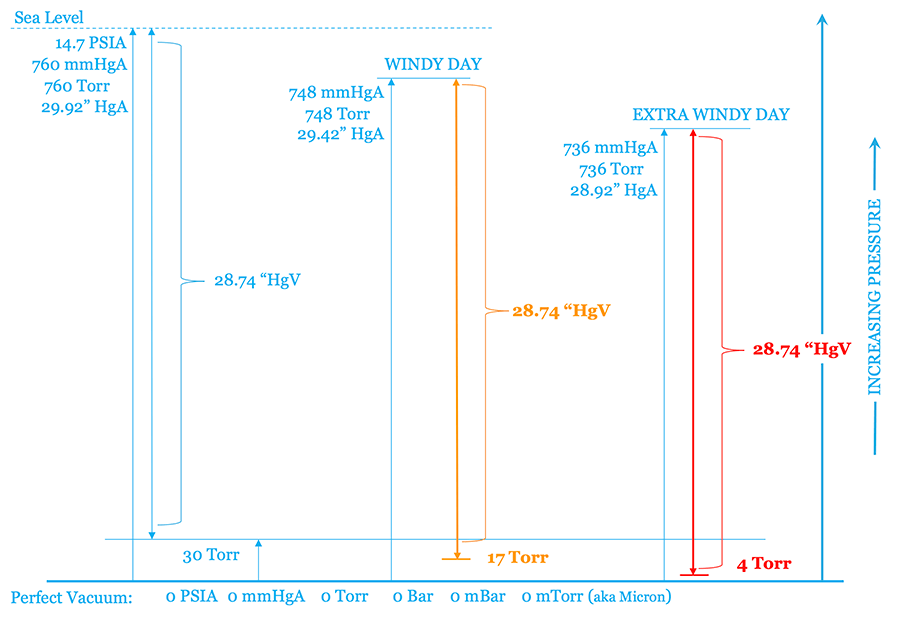
Here, we’ll note that another extremely important thing to consider is the application. In the electronics industry there is a need for oil-free air and gas compression systems.
Clean Dry Air (CDA) systems in electronics facilities are nearly without exception. Designed around two-stage oil-free rotary screw air compressors and multi-stage centrifugal compressors with dual tower desiccant/molecular sieve dryers operating at -80F or -100F PDP. Then finished with filtration elements targeting particulate size to the hundredths of a micron. This extremely high-quality requirement is based on the need for completely oil-free air to be entering the clean-rooms of the world via the tooling.
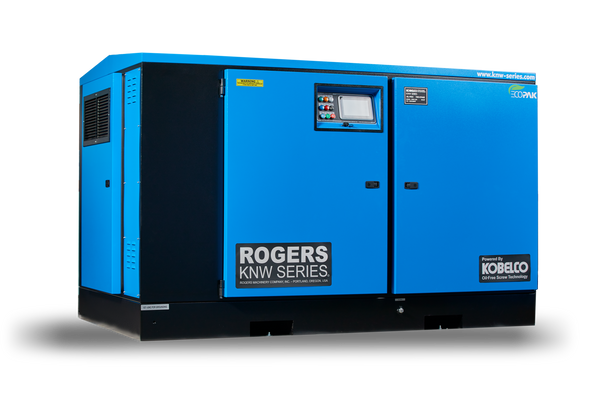
The fine vacuum requirements of the clean-room have long utilized oil-free rotary screw or oil-free multi-stage claw vacuum pumps operating to the mTorr. Entire business sectors dedicated to the manufacture and support of these oil-free vacuum pumps are required.
House Vacuum systems, including Wet Vacuum & Arsenic Vacuum and their related applications are all supplied as inherently Oil-Free multi-stage turbines.
And so it goes with the electronics industry’s Process Vacuum systems. Similar to CDA, the pitfalls of a lubricant-sealed compression element carry many costs and risks. Semiconductor Fab design engineers have for decades agreed that these risks exceed the value provided by decreased power costs and a marginally decreased one-time capital expense.
The risks of an oil lubricated design:
- Oil back-streaming toward critical fab-level production equipment, either by natural occurrence or inevitable mechanical valve failure, causing irreparable harm to the product
- Oil carry-over from lubricant-sealed pumps into the fab’s scrubbed exhaust system
- The aggressive, solvent-based nature of the Process Vacuum application’s gas mixture creating a documented, rapid degradation of oil, internal and critical to the reliable and low-cost operation of a lubricant-sealed vacuum pump
It has been, and remains to be clear, that PVAC systems should maintain an oil-free design.
There are plenty of fantastic application fits for lubricant-sealed vacuum pumps out there in the world, it just doesn’t make sense to risk oil-sealed technology in this one.
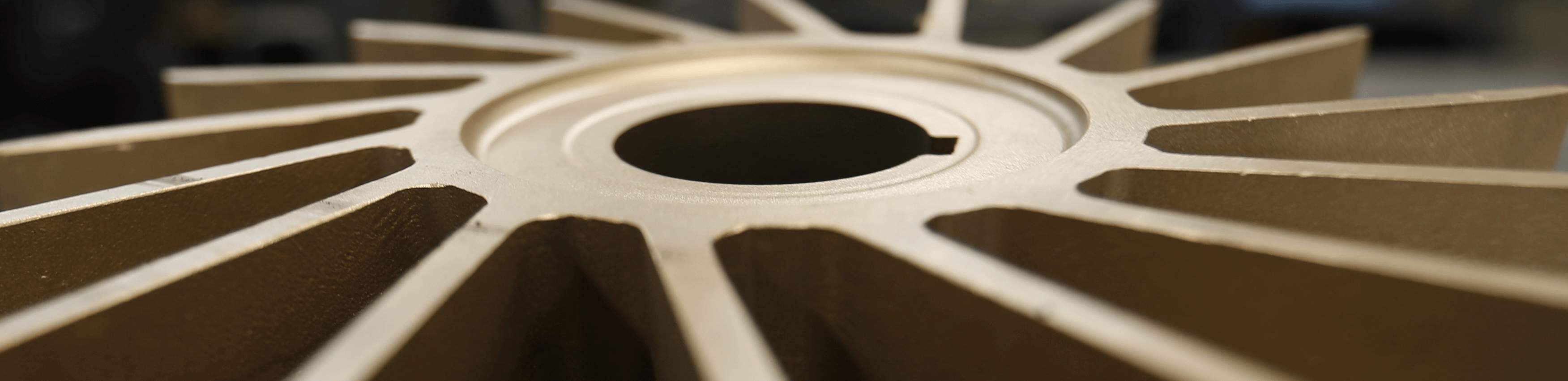
The nature of the water-sealed liquid ring vacuum pump makes it an ideal fit for the PVAC application where multiple processes with varying process gasses and condensable vapors are simultaneously being conveyed toward the vacuum pump inlet.
The relatively large internal clearances, coupled with the natural gas “scrubbing” action which occurs within the liquid ring chamber as it is constantly being flushed with treated, industrial water, make for extremely reliable operation, so long as the water quality is monitored and kept within tolerances.
A full-recirculation service fluid system coupled with introduction of new industrial water as driven by real-time conductivity analysis of the onboard water quality, will reduce the overall chilled water requirement of a liquid ring pump to that of any other water-cooled vacuum technology.
Once a liquid ring system is properly commissioned and put online, it can be kept operating for decades with little more than regular motor and pump bearing grease maintenance and intermittent heat exchanger cleanings, when coupled with the afore mentioned water quality package.
In talking with Sam, it was apparent he understood the reliability benefits of a liquid ring vacuum pump in his specific process application. After a site visit to New Mexico and a walking tour of the system, we dove into the performance specifics.
Like all vacuum pumps, Sam’s Rogers Vacuum Systems’ RVS.LR PVAC pumps operate on a performance curve that is dependent on the inlet pressure to the pump. The pumping capacity, given in terms of volumetric flow (ACFM), is relatively stable over the range of possible sub-atmospheric inlet pressures until which time that pressure becomes too low for the pump to be able to maintain the differential pressure across the pump. It is at this point that the vacuum pump loses pumping efficiency and the capacity of the pump degrades, sometimes quite dramatically, as it continues to attempt to pull deeper and deeper into vacuum.
This area on any vacuum pump is often referred to as the “knee” of that vacuum pump’s performance curve. Every positive displacement vacuum pump has one. Depending on the pumping technology, operating speed, pump design or other factors, the knee can be more or less shallow with the drop in pumping capacity falling more sharply, certain pump technologies have an ability to retain pumping capacity deeper in vacuum than others while other types have the capability to have a higher overall flowrate.
The Rogers Vacuum System the had been supplied for this application utilizes a SIHI liquid ring compression element in its design. The performance curve of each of the identical five vacuum pumps appears below.
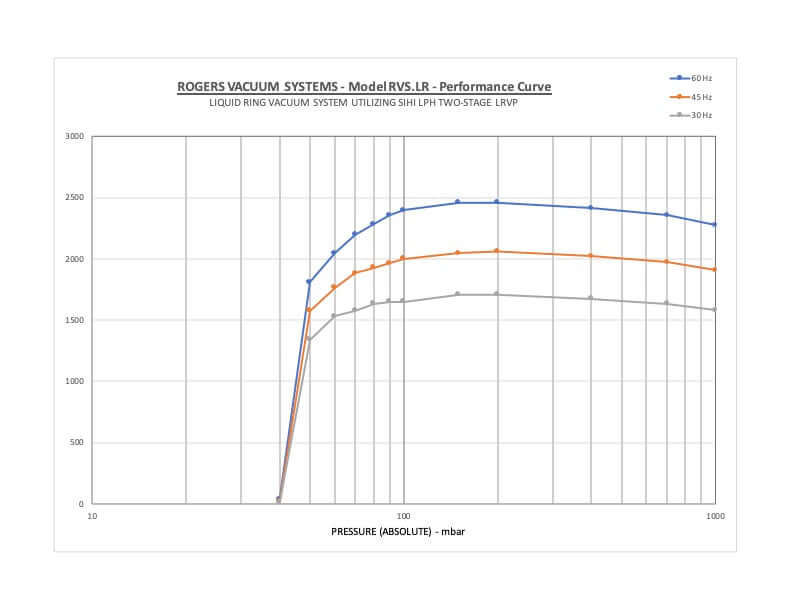
Please take note that this performance curve is appropriately displayed in terms of Absolute Pressure at the inlet of the vacuum pump and not in terms of Differential Pressure, eg. “HgV. Recall that the tooling in Sam’s fab requires a certain differential pressure at the vacuum pump in order to safely maintain production operations.
Sam’s fab’s PVAC set-point is targeted to be 23.5 “HgV. At site installations at Sea Level, that probably wouldn’t seem like much; given that the barometer at sea level reads 29.92 “Hg-Absolute (or 1013 mbar). In fact, if this installation were at sea level, in order to achieve a differential pressure of 23.5 “Hg, the inlet of the pump would need to operate at 6.42 “Hg-Absolute (or ~217 mbar). At this high of a pressure, the RVS.LR would have a pumping capacity of just under 2500 ACFM.
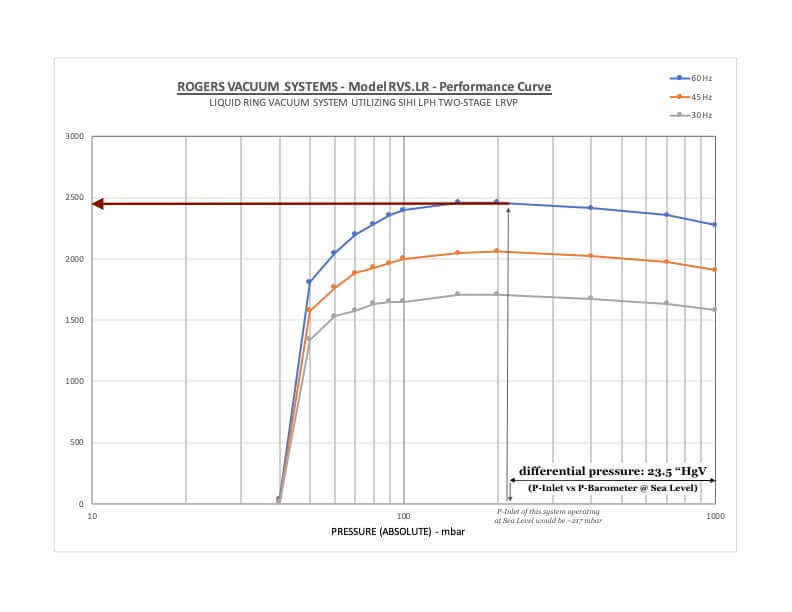
But recall that Sam’s system is installed in New Mexico, situated at an altitude of about 5,300 feet above sea level where the barometer on a typical weather day reads around 24.9 “HgA (or ~843 mbar). There is about 170 mbar less barometric pressure available to work with at this site elevation than at Sea Level, therefore instead of maintaining an easy 217 mbar of pressure at the inlet of the RVS.LR PVAC pump, the system must instead maintain a significantly lower 47 mbar pressure in order to maintain the same differential of 23.5 “HgV between pump inlet and local barometric pressure.
From the chart below, you can see that the lower pressure at which Sam is required to operate his system has resulted in significantly less pumping capacity, now around 1700 ACFM, than if the system were installed at sea level.
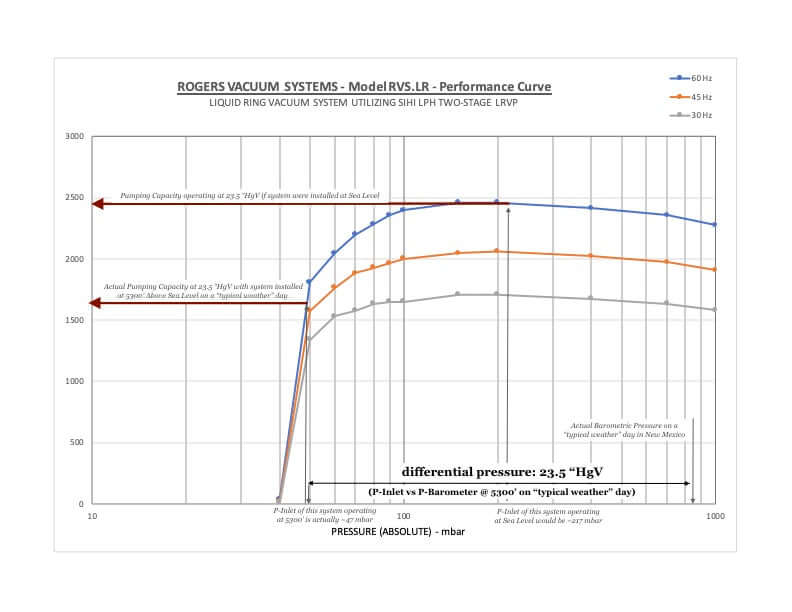
Now let’s consider the matter of work to be done on the process gasses that are being conveyed to the inlet of the RVS.LR. Specifically, the rarified mass of gas that must be compressed up to local atmospheric pressure so that it can be carried away from the pump exhaust. If we look to the Ideal Gas Law of PV = nRT, we can quickly draw out the inverse relationship of Pressure to Volume through a little algebra.
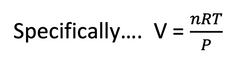
Let’s now divide both sides of the equation by time and consolidate the IGL constant with the recognition that our gas mixture will be the same molecular make-up regardless of its operating temperature or pressure. These modifications to the equation allow us to tease out the relationship of flow rates to each other, in this case Volumetric Flow as it relates to Mass Flow
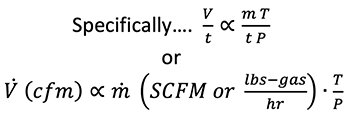
This last form of the equation gets us to the point, that Volumetric Flow is inversely proportional to Pressure when assuming that Mass Flow and Temperature are fixed. Specifically, if the inlet pressure at the vacuum pump is halved, then the Volumetric Flow must double so that the same amount (mass) of process gasses at the same temperature can be compressed up to atmospheric pressure and carried away through the exhaust.
Notice now that Sam’s five existing RVS.LR PVAC systems are quite often operating “past the knee of the curve” in the vertical portion of this vacuum technology’s capacity range.
Putting these two thoughts together, we can see that Sam is in double trouble. As Sam is requiring ever increasing volumetric flow from his vacuum system in order to just process the same amount of mass flow at a lower pressure; he is in fact getting less and less volumetric flow from the pump as it dives closer toward perfect vacuum.
Unfortunately for Sam, we were still not even done with the bad news yet. You may know that Hot Air Balloon enthusiasts who flock to Sam’s area enjoy the cold morning rare air, as nature creates the large temperature differentials desired to provide lift to the Wizards of Albuquerque.
What you may not know is that there are also relatively stable wind currents due to the prevailing weather systems and the surrounding mountains which also make exploration of the skies by Hot Air Balloon somewhat less difficult.
Criss-crossing wind currents at varying altitudes allow the balloon’s pilot to rise to one altitude and head out east. Go a little higher, now perhaps you’re headed Northwest. Drop down below the pair of these breezes and now say you’re headed South returning to your starting point.
Now imagine these same winds as they push and pull on the atmosphere in the entire area, and not from the expansive and breathtaking view of a basket, but instead from Sam’s office chair as he watches the barometer trend create a roller coaster profile as it marches on minute by minute. (REF: https://barometricpressure.app/albuquerque)
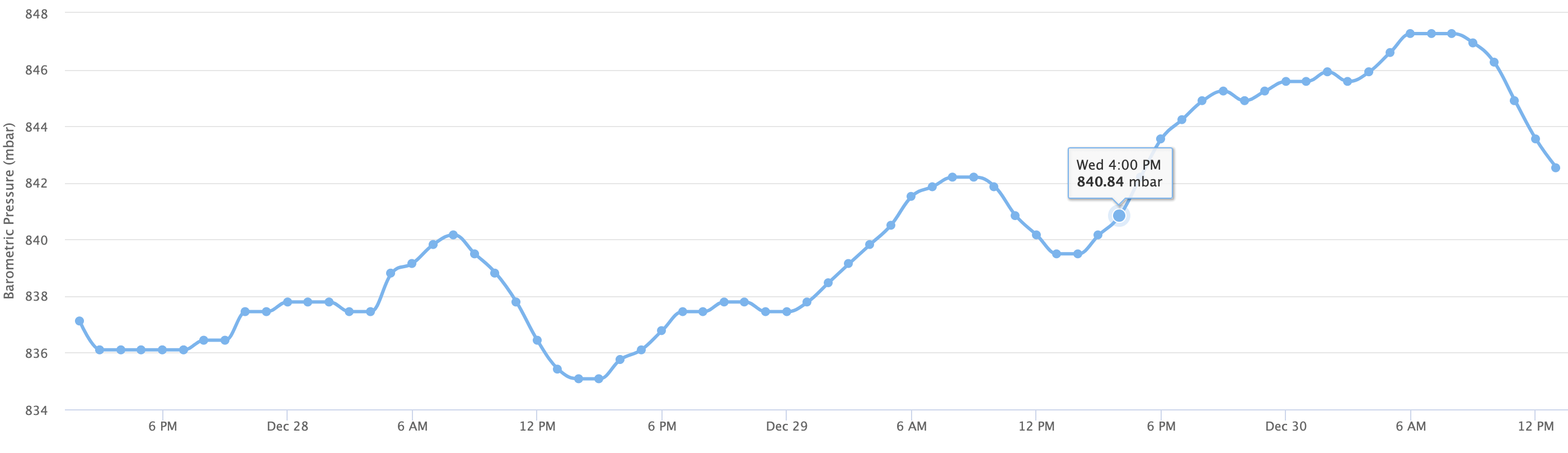
As it turns out, Sam’s site has one of the most active barometers in North America. Often seeing fluctuations of 10 to 12 mbar in just a few hours’ time.
So, what does this have to do with the PVAC System? Well, actually, quite a lot. Dare I even say; because of what Sam is asking of his PVAC system, nearly everything related to performance and control of his five RVS.LR’s revolves almost exclusively around the weather. Here is why.
If one of the five RVS.LR systems, on a “typical weather” day is performing at about 1700 ACFM volumetric flow; then what happens on a “high pressure” day, as was the case on December 30th from the trend shown above?
The PVAC controls have, say around 10 mbar more atmospheric pressure to work with; and therefore for the dP of 23.5 “HgV to remain constant; the inlet pressure to the vacuum pump will rise the same 10 mbar. This seemingly small change in the barometer allows the RVS.LR to gain pumping capacity to around 2050 ACFM, or just over a 20% increase in performance.
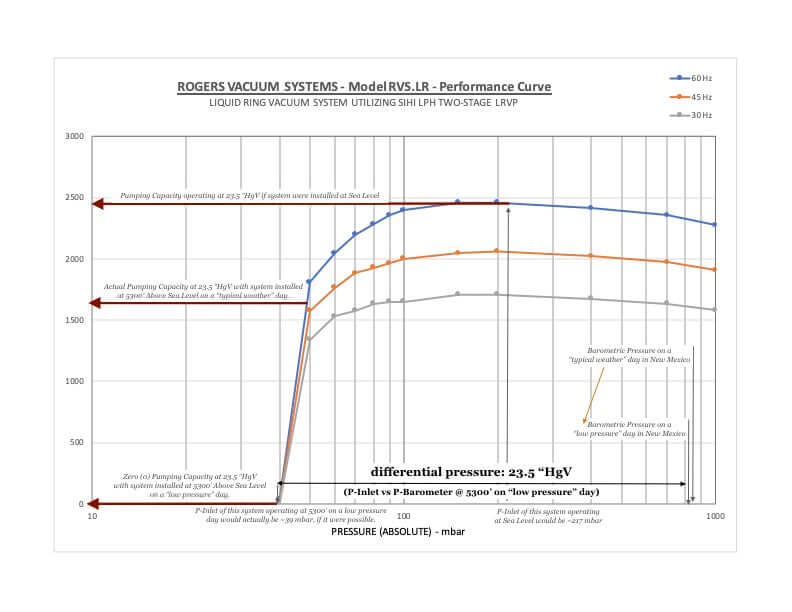
Now what about the other direction? What happens if the weather turns sour, and a “low pressure” system moves in? Should the barometer drop the same 10 mbar from “typical”, the PVAC system now has 10 less atmospheric mbar available and, in order to maintain the same 23.5 “HgV differential pressure between the vacuum pump inlet and the now-lower local atmospheric pressure, the inlet pressure must drop by the same amount.
You can see the result above on the performance curve. Dropping the inlet pressure at the inlet of the RVS.LR PVAC system to 40 mbar would require the removal of the entirety of the gas mass demand load being processed by the vacuum pump.
Alternately put, the volumetric pumping capacity of the system falls to Zero (0) ACFM at 40 mbar inlet pressure. With all of the right operating conditions besides, the pump might actually be able to achieve such a low pressure; but it would have to be completely blanked off at its inlet in order to get there.
So here was the rub. We had found our dilemma. A half dozen or so years previous, Sam recalls having had increased the target setpoint up to 23.5 “HgV. It was able to get there much of the time, so it seemed a fine place to operate. But the system had been designed for a higher inlet pressure (lower dP) in order to perform to the peak of its ability.
Whether it was a new line that was added that had a slightly higher pressure drop and the setpoint had to be increased in order to accommodate, a new demand that required a higher differential, or some other circumstance which caused the change, Sam found himself with a system that was being asked to do something that it wasn’t perfectly and efficiently designed to do.
The Analysis
Sam’s intuitive question in our first phone call, “Can I get price and availability for an identical RVS.LR system?” is plenty justifiable. Having all existing units online and running 100% and unable to meet setpoint, he was, indeed, “out” of vacuum. They no longer had full redundancy in their system. It only stands to reason that Sam needed another vacuum pump to add into the mix.
Let’s play that solution out, on paper, while looking again at the performance curve. This time, however, we’ll put all five (5) PVAC systems online and running at full capacity (60Hz) instead of looking at just one on its own. Pretty simple multiple to do this, totaling all their pumping capacities together and displaying the sum on the y-axis.
Let’s also assume we are operating on one of the “low-pressure” days that we’re worried about. Maybe not the lowest low, but a ‘normally occurring’ low pressure day. Looking up the historical trends of the site, we see the local barometer over the previous 12 months ranging from 24.15 “HgA to 25.33 “HgA (or about 821 to 858 mbar). Let’s pick the below-average value of 835 mbar for our performance analysis.
Also, from Sam’s own analysis of his trends, we know that his system is regularly unable to meet the target setpoint dP of 23.5 “HgV. On these low pressure days, we commonly see the vacuum system achieve somewhere around 23.2 “HgV instead. Putting all of that together, we got a typical total system performance as shown below.
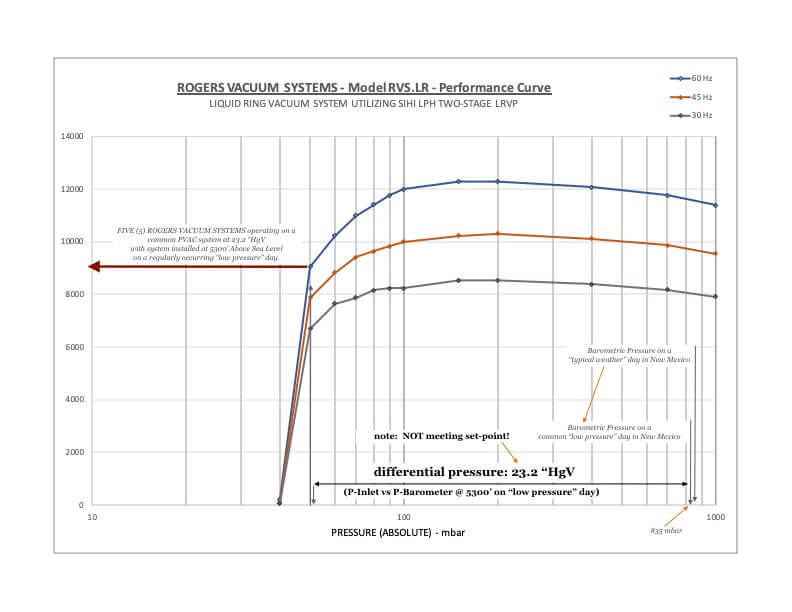
So with all five (5) of Sam’s RVS.LR systems online and operating below the desired setpoint of 23.2 “HgV; we see that the whole system has a combined volumetric pumping capacity of about 9600 ACFM.
We can now calculate the mass of gas that these pumps are compressing up to local atmospheric pressure by converting volumetric flow (ACFM) to mass flow (SCFM or # of air/hour). Again using the Ideal Gas Law as the root of this calculation and assuming room temperature gas of 68F & gas inlet pressure of 50 mbar, we estimate that the total mass flow load of the entire PVAC system at Sam’s facility commonly sits somewhere around
Next, we’ll look at what will happen should we add that 6th RVS.LR PVAC system into the mix.
Let’s assume that all the facility’s tooling and vacuum requirements remain unchanged during the installation of the 6th vacuum system. That is the same as saying that the load, always given in terms of mass flow, remains unchanged. The only thing we’re hoping to do is hit the vacuum set-point on a regularly occurring “low-pressure” day while still having the new, larger, vacuum system processing the same 2,140 #-air/hour.
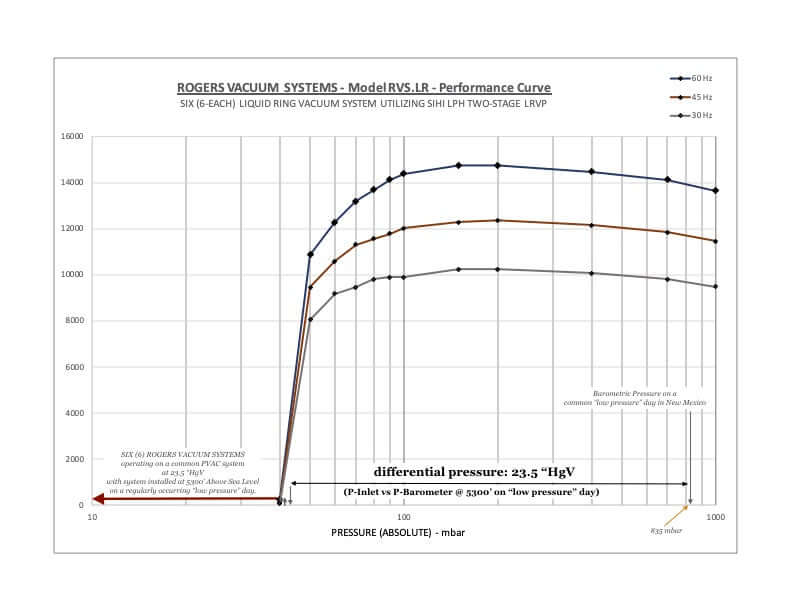
As you can likely already tell from the “new and improved” six-system performance chart above; there really isn’t much improvement that a sixth system will provide. If one were to trust operating in this steep portion of the vacuum pump’s performance curve, you might be able to have a little load (calculated to be about 43 #-air/hour) with 6 units online while maintaining 23.5 “HgV; but nowhere near the 2,140 #-air/hour the facility’s PVAC system demands.
Let’s look at this another way. Recalling from earlier that the lower in pressure the inlet of the pump drops requires that the volumetric capacity gets ever and ever proportionally larger; just how much volumetric pumping capacity does the system need to provide in order to compress the 466 SCFM (or 2,150 #-air/hour) up to local atmospheric pressure?
Reversing the calculation and starting with mass flow load in SCFM to calculate ACFM-Required, we find that in order to do the work demanded by Sam’s facility, we need a PVAC system volumetric pumping capacity of about 12,350 ACFM when operating at 39 mbar.
By taking this value and then performing a mass flow balance to the actual performance curve of the system with a future 6th PVAC pump, we can model that the actual operating point of that system would be at a pumping speed of just under 10,000 ACFM while holding an inlet pressure of about 48 mbar, or about 23.25 “HgV as it relates to the barometer on our ‘normally occurring’ low pressure day.
Put a different way, adding a 6th RVS.LR process vacuum pumping system would only see gains in vacuum of about 0.05 “HgV over the 5 PVAC system arrangement.
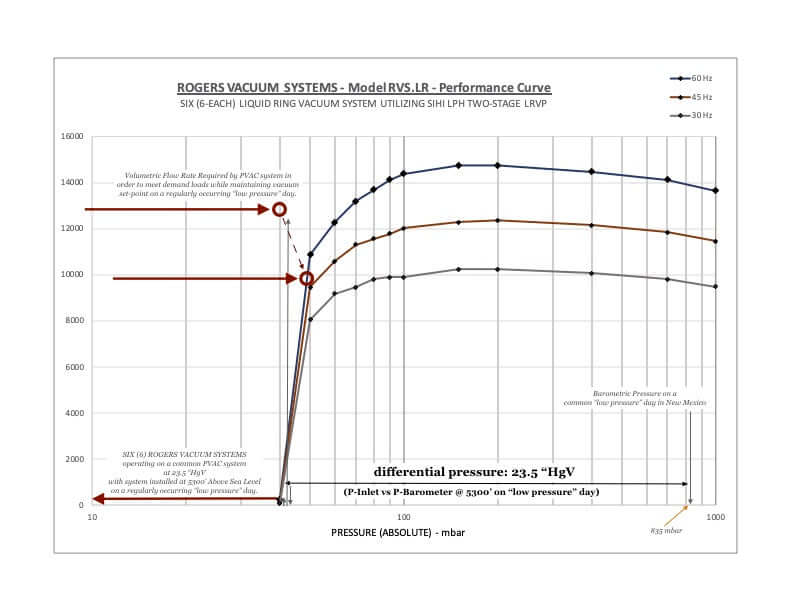
Additionally, because Sam would be still operating his system in the extreme vertical portion of the speed curve and past the knee, it is very difficult to understand exactly what will happen since extremely minor changes in inlet pressure result in vastly increased or decreased pumping capacities. This is without discussing the other negative ramifications of operating a liquid ring pump too low in pressure which includes harmful cavitation and even freezing the service fluid into ice.
While we are vastly undersized at the desired operating pressure, it is also easy to see that we’re also not far off. If only the inlet of the vacuum system could operate at just a couple dozen mbar of increased pressure, then even the existing system of five would have adequate and even excess pumping capacity to meet the system demands.
The inlet pressure to Sam’s liquid ring pumps simply needed a bit of a boost.
The Solution
Contrary to how some folks attempt to describe the nature of vacuum and vacuum pumping equipment; vacuum is NOT “negative pressure”, and a vacuum pump is NOT an “air or gas compressor running-in-reverse.”
Vacuum pumps are, in fact, also compressors, taking a low (sub-atmospheric) pressure into their inlets, compressing that gas internally and then discharging to a higher (atmospheric) pressure. The parts and pieces of a vacuum pump and an air compressor are therefore very similar and laid out in a similar order internal to the equipment skid.
There are aspects of each, however, that are quite different. The mass of gas that a vacuum pump compresses through it is extremely low as compared to a similarly sized gas compressor, while the compression ratio demanded of a vacuum pump is conversely much higher. There are a huge number of compression technologies available in both the positive pressure and sub-atmospheric realms for targeting specific application needs and commercial concerns. (view our Custom Process Solutions).
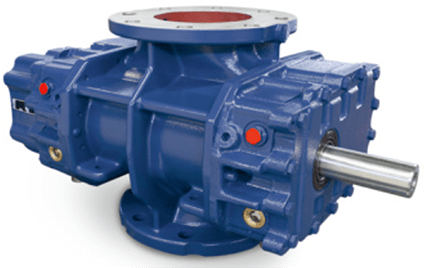
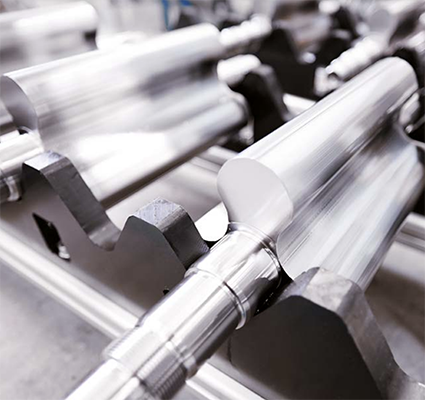
Rotary lobe blowers have long been a solution for low to moderate pressure gains at a wide range of flow rates. They have an oil-free compression chamber, as is required by Sam’s application & site maintenance requirements and can be manufactured in extremely large sizes rather economically, due to their simple design and relatively large internal clearances.
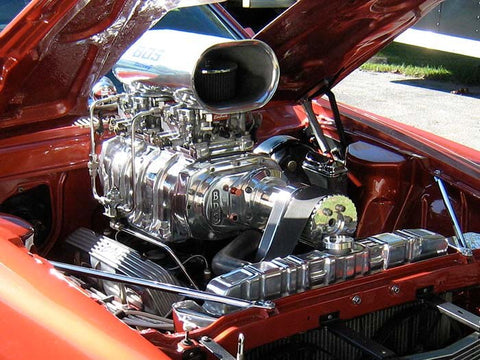
Known most commonly throughout industry for their positive pressure applications such as wastewater aeration, pneumatic conveying or that turbocharged AMX in your neighbor’s driveway, they have also been applied for vacuum applications with increasing regularity.
While rotary lobe blowers are commonly used as a standalone vacuum solution for vacuum conveying of materials such as grain or powders; they have also been applied in multi-staged vacuum systems serving process-related functions for decades.
When engineering a new Custom Process Solution, Rogers Machinery utilizes several different manufacturers’ compression elements within their designs. The Rogers Vacuum System packages (MODEL RVS.RL) designed and supplied for Sam and his fab, utilize Aerzen HV vacuum boosters.
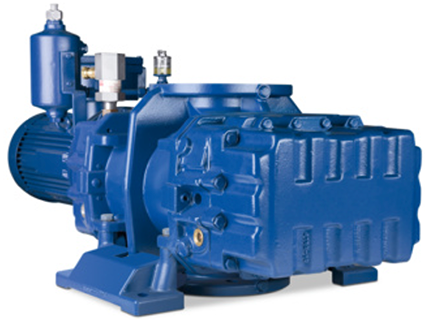
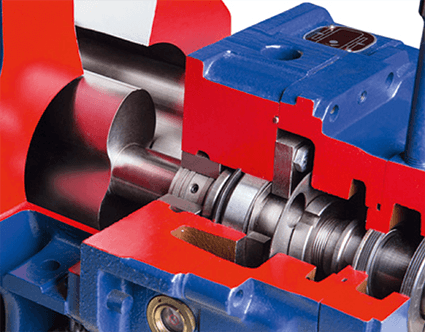
A typical “Hybrid” vacuum solution is composed of some type of mechanical or “backing” vacuum pump which provides the proverbial heavy-lifting and then some number of stages of “High Vacuum Boosters” installed upstream of the backing pump.
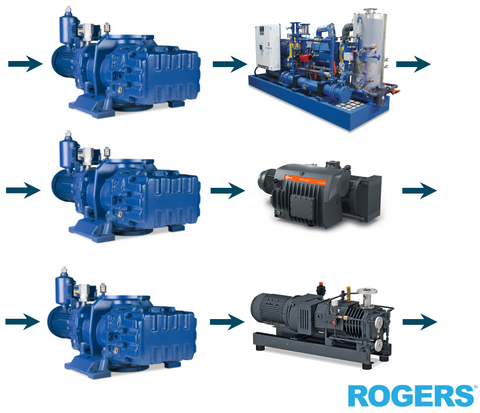
In building out such a multi-stage hybrid vacuum system in your mind, it may be helpful to first think of the stages of compression of a high-pressure air compressor system for reference.
If an application were to call for six or seven hundred PSIG, very likely, a standard 100 or 150 PSIG air compressor, possibly supplied with standard filtration and drying systems. Then downstream of that, somewhere following in the system, would be a reciprocating booster compressor. The job of the booster compressor would be to take the 150 PSIG air pressure into its inlet and increase to the ultimate pressure of 700 PSIG, or whatever the application demanded.
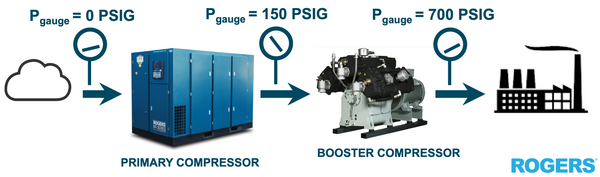
The converse for a Hybrid High Vacuum system is also true. Just as with the multiple-staged compressor system, the primary backing vacuum pump is furthest away from the factory floor with ever increasing stages of vacuum boosting occurring the nearer that the process requirement becomes. The weird trick here is the direction of gas flow is opposite than that of the compressor system above. Shown above, the boosters in a compressor system are downstream of the primary compressor, as the gas nears the process application.
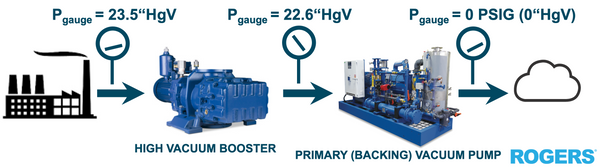
The boosters in a Hybrid vacuum system are upstream of the primary backing pump, as the gas load emitting from the process application progresses toward atmospheric discharge. This is, of course, due to simple physics. High pressure always flows to low pressure; and we use compressors to increase the low pressure to high in order to propagate that flow. It can seem confusing since we so often speak in terms of differential pressure while calling it “vacuum”.
When you look at this same chart in terms of absolute pressure, instead of differential pressure from atmosphere (aka vacuum), it clearly becomes the same situation as with the gas compressor. That is, low pressure is increased to ever higher pressure through the various stages of the hybrid vacuum system.
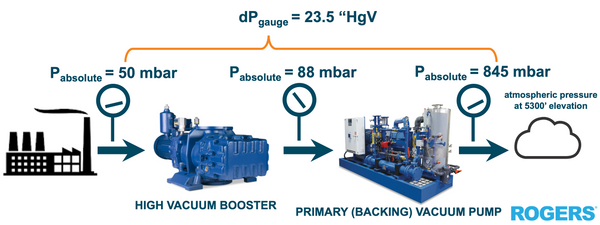
A little bit more on vacuum booster compression ratios.
In “fine” vacuum process applications, say a reaction chamber operating at 5 to 10 mTorr, it is not uncommon to see compression rations of 10::1 or even 25::1 or maybe even higher. Boiling it down, these high compression ratios are allowable at these low pressures because the gas is so extremely rarified that there is very little mass to compress and subsequently generate heat.
With increasing vacuum booster inlet pressures, the gas is becoming more and more dense and therefore the opportunity for higher and higher temperature rise. We therefore see lower booster compression ratios, such as 3::1 or even down to 1.5::1 with booster design inlet pressures in the roughing realm of 30 to 60 mbar.
At some point, the inlet pressure to the vacuum booster becomes high enough that the allowable compression ratio falls too near to 1::1 for the booster to be an economically viable solution.
Back to Sam...
If you recall, he needed more volumetric flow while operating deeper in vacuum but was getting substantially less. To be specific, he needed 12,350 ACFM when operating at 39 mbar.
Let’s throw the above demand requirement onto his existing five (5) RVS.LR system’s combined performance chart. Let’s also assume that we safely select a booster sized for performance at a 1.75::1 compression ratio.
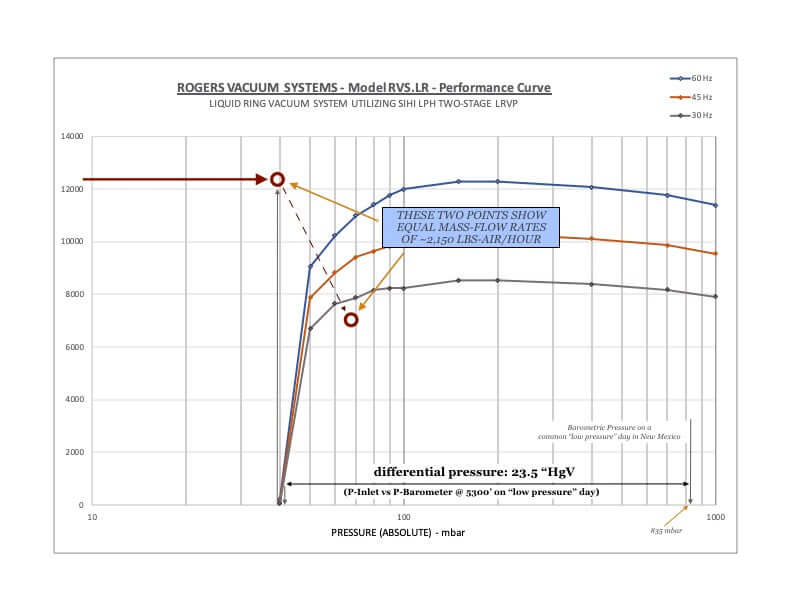
By increasing the operating pressure at the inlet of the backing pump through the use of a rotary lobe vacuum booster by a factor of 1.75, we have also decreased the volumetric flow required from the backing system by the same factor if we assume that the mass flow load required by the factory doesn’t substantially change.
The results on the chart show the extreme benefit of a vacuum booster in this situation. Without boosters, the five (5) RVS.LR systems all running at 100% cannot meet the demand requirement while maintaining set-point. The desired operating point of 12,350 ACFM at 39 mbar is outside (above and to the left) of the vacuum systems performance capability.
With a booster installed upstream of and increasing the inlet pressure to the liquid ring systems, however, not only is the new desired operating point ~7,060 ACFM at ~68 mbar inside (below and to the right) the maximum capability of the RVS.LR system; it is also inside the minimum capability of the five (5) vacuum pumps running at their minimum speeds. This means that all liquid ring systems will need to run to their minimum speed while some shut down completely, in order to match vacuum capacity to demand.
All Together Now
Sam’s situation is dynamic and complex. The desired operating vacuum, site elevation and variable barometer create (ahem) a perfect storm of circumstances which greatly impact the performance and operation of his process vacuum system.
It goes even deeper than this, though, when you realize that the five (5) RVS.LR process vacuum pumps we’ve been speaking about are installed on two separate, semi-independent, sides of a combined vacuum system. Side A uses two (2) RVS.LR units while Side B uses three (3).
In sizing and applying the appropriate vacuum boosters, it was desired to have like components for continuity of the installed equipment. Just as with the five (5) identically supplied RVS.LR systems, Sam wisely didn’t want dissimilar boosters for maintenance personnel to need to manage. He also, of course, required full redundancy on all sub-systems.
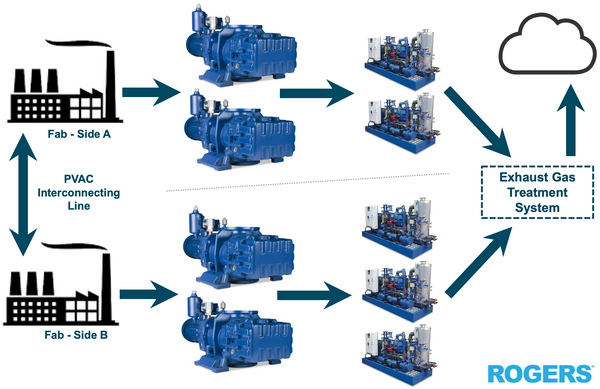
Lastly, because of the possibility of aggressive solvents and other process gasses in the process vacuum gas stream (Recall that these are the same gasses which would solve and break down vacuum pump oil internal to any lubricant-sealed vacuum pumping technology); Sam’s RVS.LR vacuum pumps cannot exhaust directly to atmosphere. The gas stream must first be treated prior to atmospheric discharge.
An automated control scheme for the new boosters needed to be created to include all the design goals of the subcomponents that we’d selected.
Control System Requirements
- Complete Redundancy
- Able to accommodate any system subcomponent, Booster or Backing Pump, faulting offline without warning…
- …or purposefully being turned off for maintenance.
- Variable and Unknown Exact Demand Load
- Side A: ~1000 lbs-air/hour (~220 SCFM) … plus or minus?
- Side B: ~1150 lbs-air/hour (~250 SCFM) … plus or minus?
- Variable Barometer … a Roller Coaster!
- LR backing pump utilities affecting LRVP performance
- Potential exhaust pressure fluctuations
- Potential for variable Chilled Water
- Potential for full-recirculation heat exchanger fouling
- Multiple combinations of boosters online with backing pumps online
- (1) RVS.RL Booster ‘ON’ & (1) RVS.LR Backing Pump ‘ON’
- (1) RVS.RL ‘ON’ & (2) RVS.LR ‘ON’
- (1) & (3); (2) & (2); (2) & (3); etc. etc...
- Save utility cost by running RVS.LR Backing Pumps at reduced speed
- Electrical energy is saved by operating at or near minimum speed
- Chilled water demand is decreased at or near minimum speed.
- Single Control Input
- Entire system to have Variable Speed Control
- Targets a fixed differential pressure setpoint of 23.5 “HgV
When talking control of a Hybrid Vacuum System, the order of operations and control of the staged components is critically important. To build this up, let’s first consider initial start-up of a completely offline system, one that has yet to establish any vacuum because the “GO” button has not yet been pushed.
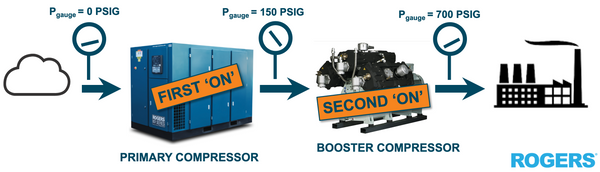
In the multiple staged high-pressure compressor system, which we previously discussed; it is relatively logical to understand that operators of that system would need to start the primary gas compressor first to establish the 150 PSIG initial pressure that the secondary booster compressor requires at its inlet. Only then would the booster compressor be allowed to start, ingesting the previously compressed gas at its inlet and then compress up to the final desired pressure of 700 PSIG. In this case, the starting sequence is in order according to gas flow direction.
The Hybrid Vacuum System is the same; almost. Startup sequence is just as critically important. You’ll see, however, in the image below that the starting sequence in the case of Hybrid Vacuum systems is opposite of the gas flow direction. That said, the underlying methodology is identical.
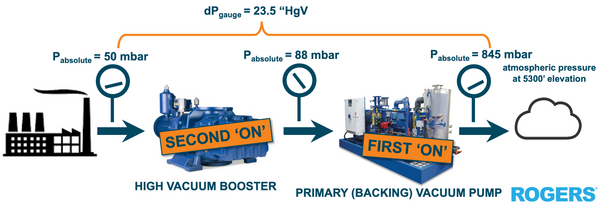
The RVS.LR backing vacuum pump must start first, evacuating the vacuum distribution lines of air and process gas upstream to a predetermined design cut-in pressure. Only then can the upstream booster safely start and operate. You can see this cut-in pressure on the attached combined Hybrid System performance curve below, showing one (1) RVS.RL Booster online and running at 100% (below 200 mbar inlet pressure) and backed by a single (1) RVS.LR backing vacuum pump online and also running at 100%.
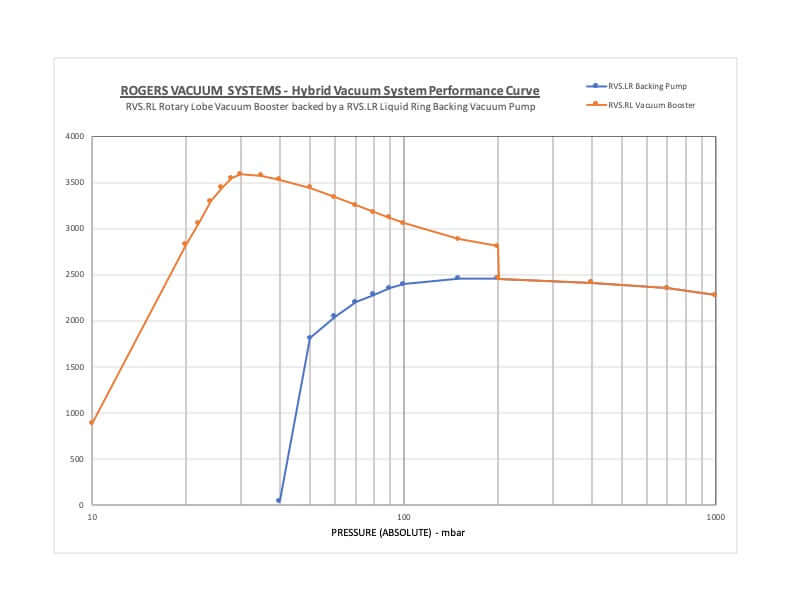
Incidentally, in this performance chart you can also easily see the total system benefits of adding a booster to this backing pump. At a time when this system needed increased volumetric flow while also operating at a lower pressure (deeper vacuum), the RVS.RL rotary lobe booster provides exactly that. In effect, the booster acts as a multiplier to the RVS.LR backing pump.
So regarding controls, it’s the same; except different. In compressor systems, the compressor is looking just downstream of itself for control input. In vacuum systems, the vacuum pump is looking just upstream of itself for control input. And in multi-stage hybrid vacuum systems, with multiple sets of boosters upstream of the backing pump, each successive upstream booster is started at the time that each new permissive cut-in pressure is reached.
Now that the system is online and maintaining the target vacuum setpoint, we needed to ensure Sam’s system was prepared for change. A change in demand load coming from the fab, a change in barometer, one or more of the subcomponents turning on or off or any combination of the above or other factors.
Further, because the existing RVS.LR liquid ring backing pumps were variable speed controlled and targeting a fixed differential pressure, Sam’s new RVS.RL vacuum boosters must also be VFD driven. This is because if we were to slow down Sam’s backing pump while leaving the booster operating at full speed, we would certainly over compress the gas at the inlet of the backing pump. This would create too high a pressure in between the two system subcomponent stages and the high compression ratio across the booster would induce a high temperature and fault out the booster.
In a joint effort between Rogers Machinery Automation Technology and project engineers, Sam’s onsite Instrumentation & Control consultant and his own onsite operators and maintenance personnel, a control scheme was developed and commissioned to accomplish the design goals.
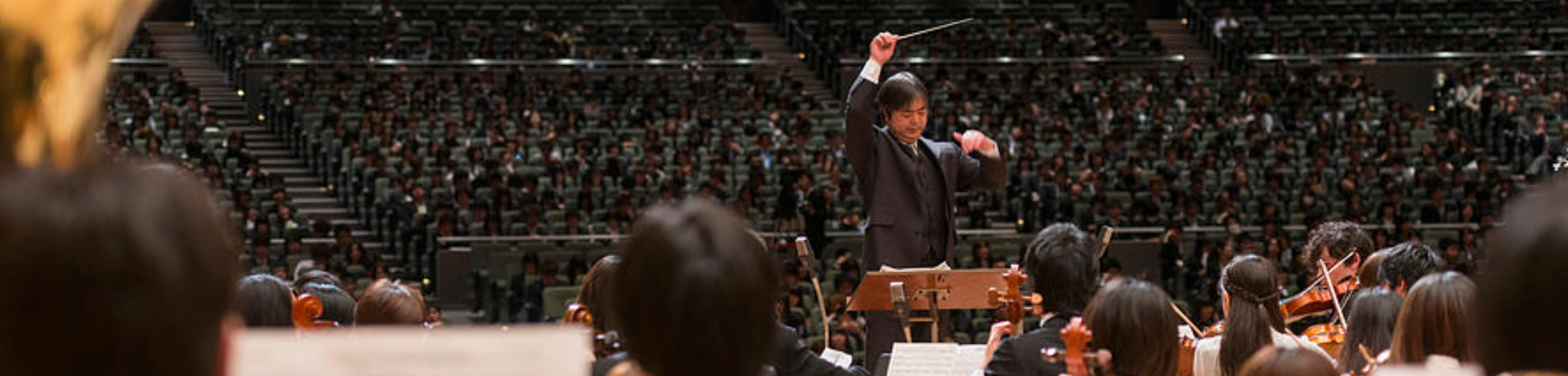
Like a symphonic conductor bringing in more wind, strings or low brass at the just right moments to the enjoyment of the clean-room, vacuum tooling audience, this controller watches the combinations of subcomponents online at any one point and adjusts the speed relationship of booster to backing pump accordingly.
For example...
Let’s say Side A is operating with two (2) boosters online with both backed by (2) RVS.LR vacuum pumps. The speed relationship between booster and backing pump is matched. For every speed increase or decrease in the backing pump, the booster has a similar proportional speed adjustment.
Imagine Sam wants to do some heat exchanger maintenance on one of his RVS.LR backing pumps. When he shuts it down, the controller recognizes that the combination of two (2) boosters with one (1) backing pump won’t work because there would be too much of a good thing. Both boosters would over-heat and high temp out. So the controller shuts down one of the boosters automatically and the Hybrid pair left online maintains the 1:1 speed relationship.

But what about Side B? Let’s say at that moment a single booster is online but is backed by all three (3) RVS.LR vacuum pumps on that side. With all three online, they’re all now running at their minimum speed of 50% because of the multiplication effect of the booster. The single booster, however, is running somewhere closer to say 85% of its speed while processing the entire load from Side B.
Because Sam flipped off one of the backing pumps on Side A, he suspects some of the fab’s demand load might need some additional help, so he makes the long walk to Side B to turn on the second booster on that side. Once online and running, the controller sees the 2:3 relationship and adjusts its speed proportions again. Now with both Side B boosters online, the unit which had been running at around 85% drops to, say 65%, while the second booster speeds up to match it. Perhaps the backing pumps speed up a few ticks to 55% or so while the Side A pump is offline for maintenance.
Even in this configuration, with a system down for maintenance, the newly boosted vacuum system still has full redundancy sitewide. That is, with (3) Side B backing pumps running at 55%, Sam could unexpectedly have one of these system subcomponents drop offline and the other two would pick up the slack without breaking much of a sweat. If that were to happen, the controller would see it and adjust the multiplication effect of the upstream boosters to the appropriate new speed relationship, now 2:2.
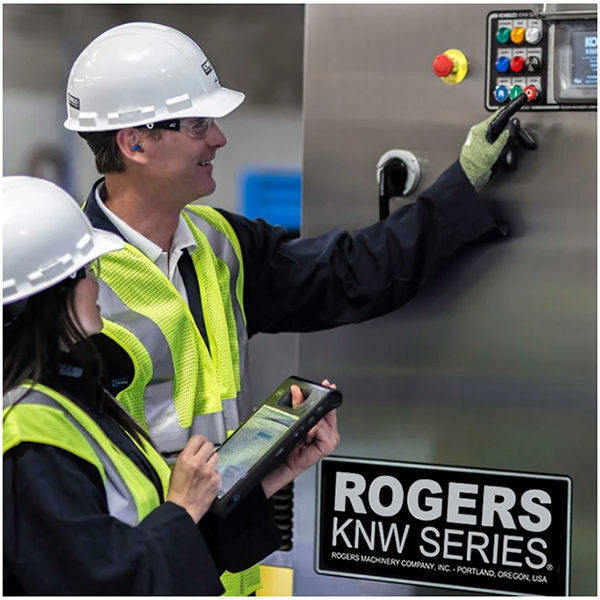
With high temperature safeties in place, the system controller has accomplished the many design goals for which it was designed.
Completion And Savings Highlights
When Sam rang us awhile back, he was in a pickle. With all his vacuum pumps online and running, he was out of redundancy. He couldn’t even turn off a pump to properly maintain it. What’s worse, he couldn’t meet the vacuum demands of the plant, which were subject to, literally, which way the wind was blowing.
By giving his existing vacuum pumps a boost with an intelligent system-based solution and customized controls; Sam now has, on average, 2 ½ spare vacuum pumps available while meeting and exceeding the plant demanded vacuum set point, all regardless of the weather.
These gains translate to:
- Over 2,000,000 kilowatt-hours of annual saved electrical energy
- 87,000,000 gallons of reduced chilled water consumption on site
- Associated cost savings easily over $200,000 per year
Not to mention the improved production and equipment reliability due to the vacuum maintained in the clean-room, and the improved maintenance capabilities of the PVAC system subcomponents.
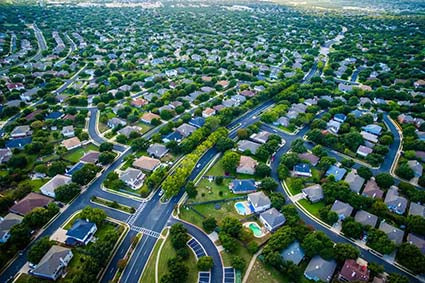
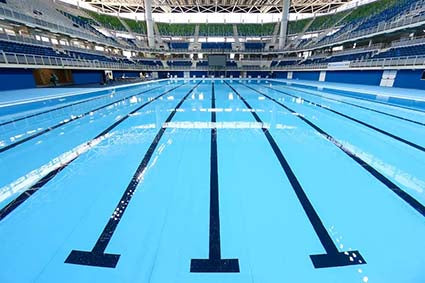
These savings are about the equivalent of powering 185 average US homes and enough water to fill about 132 Olympic-sized swimming pools every year. All of this for a project that cost about 25% more than the project Sam thought he was signing up for when he called. The insanely short Return-On-Investment of the capital expense was the cherry on top.
Written by Bryan Jensen, Corporate Projects Manager, Rogers Machinery.
Read more customer case studies from our Custom Process Solutions team.